Each era in history has its own unique signature, which both symbolises and summarises what life was like for those who lived through the historical events. We can only wonder how the events of the 21st century will be summed up when young people open their history books in 50 years’ time. Will they see the 21st century as the end of the coal industry? Will they perhaps live in a completely carbon-free world and enjoy clean air? There is no way to predict what will happen next, but we are the generation that can influence what the history books will say.
Thermal energy: the roadmap to zero emissions
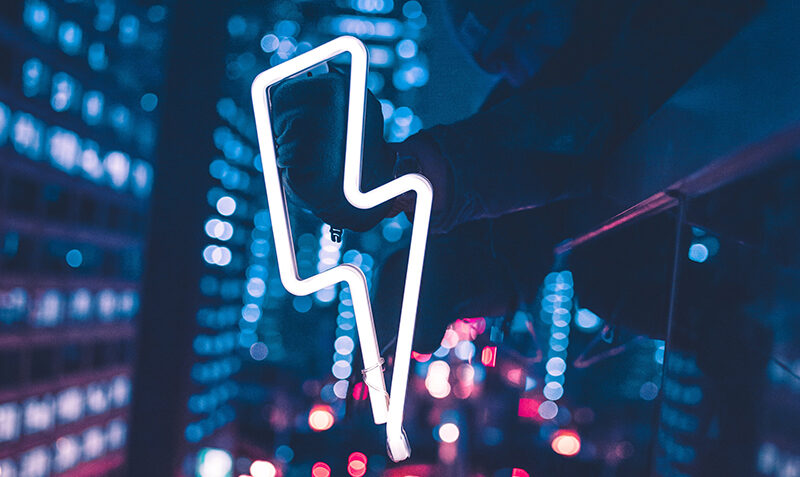
Focus on achievable objectives!
The 2015 Paris Agreement called on governments and private companies around the world to implement plans to limit greenhouse gas emissions, with many organisations setting aggressive targets such as “Zero Emissions” by 2040.
This means that industry leaders must already prepare their plants for decarbonisation. Corporate sustainability teams recognise that total electrification and renewable energy are not sustainable solutions at this time due to cost and availability. Realistically, manufacturers can comfortably cut 30% of their energy consumption by making no changes and without hindering long-term production opportunities.
One example is the food and drink sector, which accounts for a quarter of the world’s greenhouse gas emissions. Most factories were built more than 50 years ago and are simply ad hoc as time goes by, rather than updated with improved technology. As it stands, only 15% of the food and beverage industry is on track to meet sustainability targets, leaving industry leaders with a competitive opportunity to win the race to zero carbon emissions.
Steam replaces coal
One simple idea is for factories to start optimising thermal energy use within their plants. Around 80% of food factories already use steam, which means they are equipped to capture waste heat and use it to replace purchased fuel. Using a three-step process called “Circular Thermal”, it includes “de-steaming” (conversion to hot water under pressure), recovering direct heat when a positive differential temperature is available, and using industrial heat pumps to raise the temperature of low-grade heat to a useful temperature for each particular process.
Mapping the path to decarbonisation
Once plants are optimised, companies can prepare for the ultimate decarbonisation at reduced capital costs, making optimisation a practical first step. This decarbonisation roadmap takes time, patience and most importantly: the knowledge and resources to achieve the goal. There are many experts in energy efficiency to get companies on the right track, and with more than a century of experience, we’ve learned that the journey begins with optimizing current resources and minimizing waste.
In 50 years, what do we want our past to say about us? Instead of just looking ahead and scrapping everything we have, why not optimise what we have to get us on the road to a greener future faster?